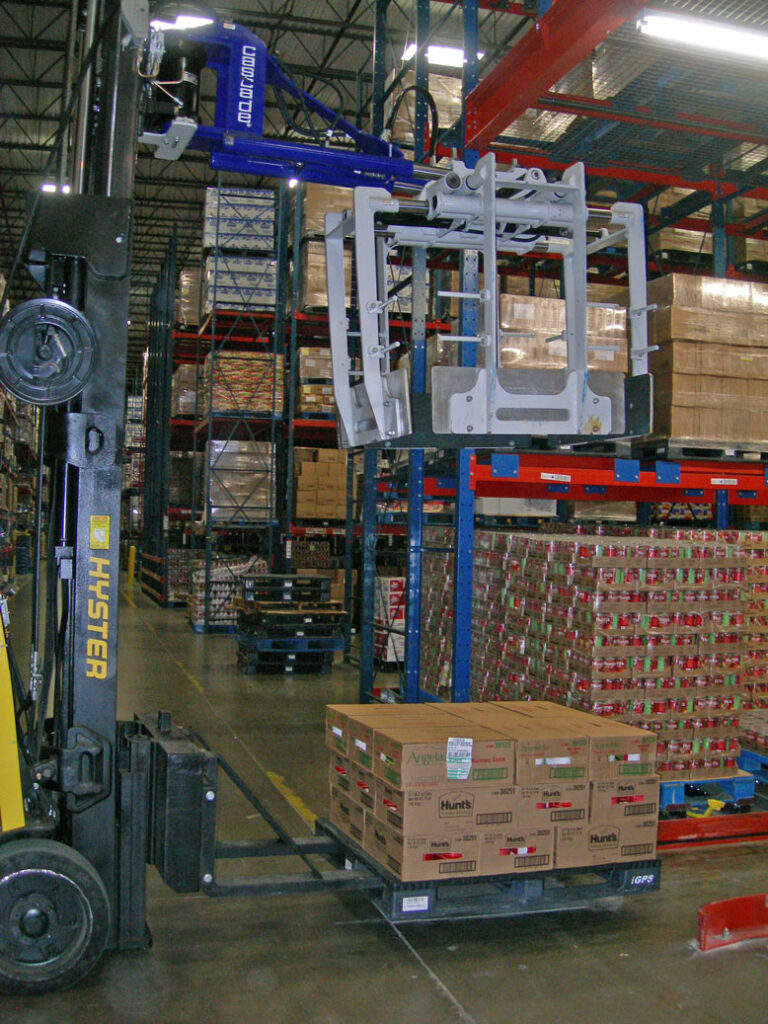
A fork truck with a layer picking attachment assembling a mixed SKU pallet.
Did you know that a whopping 63% of distribution activity, on average, is spent picking products? By contrast, shipping, receiving and other related activities only make up 18%, 13% and 6% of distribution, respectively.
Consequently, focusing on improving picking productivity is a key metric that an operation can target to measurably increase its overall efficiency. One way many warehouses are doing so, particularly in Food and Beverage sectors, is by layer picking.
A diagram of what a pallet assembled by layer by layer might look like. Every layer consists of only a single SKU.
What is Layer Picking?
Layer picking is a means of swiftly assembling a customized blend of products onto a single pallet. It is an ideal application for operations that deal with just-in-time orders or require the ability to fulfill mixed-SKU pallets of several high-volume products.
A fork truck uses a layer picking attachment to select a layer of products.
To pick, fork trucks use special attachments to handle a “layer” consisting of multiple cases of the same SKU. Picking a layer at a time in this manner as opposed to a case at a time by hand is the key to efficiency. An operator using a layer picking fork truck can out pick manual labor at a rate of 5:1. This means of handling is also safer for products and workers alike. Cases assume less risk of being damaged and physically demanding labor that causes injury to employees is eliminated. Additionally, this means workers can then be reallocated towards other important tasks as part of the overall operations instead. Cascade, a manufacturer of layer picking fork truck attachments overviews the concept perfectly in This Video.
Rack Design Advantages
Many layer picking applications simply floor stack alongside a floor mounted rail guide for the fork truck. Designing your application around a racking system, however, results in a better use of warehouse space as well as a more efficient means of replenishing products.
A layer picking application’s rack design starts with the picking aisle. Ensuring enough space is left in the aisle to maneuver the fork truck’s layer picking attachment is critical. Once the picking aisle has been established, it is ideal to form a design that replenishes products from exterior aisles for sake of productivity; this way, the picking aisle does not need to also be used for replenishment.
A Pick Tunnel Rack System for layer picking.
To achieve this, floor level lanes are typically designed with Pallet Flow Racks that are loaded from the exterior lanes. Product moves forward by means of gravity to the aisle position where layers are selected via the picking lane. Adjacent to the Pallet Flow lanes is bulk storage. Glide-In® Push Back Rack is the ideal rack type for this. For one, it is a denser solution that affords greater storage capacity and can even be used as part of an overhead Pick Tunnel for maximum storage. Its density also means the fork truck cannot accidently reach through the racking into the picking aisle, where it could disrupt picking operations. If selective racking were used, this could occur. On top of its density, Glide-In® Push Back Rack is also both loaded and unloaded from the face position, meaning all access is done from the replenishment lanes.
Learn More About Frazier’s Rack Solutions
Frazier has experience designing Layer Picking Racking Solutions for a variety of applications. Whether you are a veteran or a beginner looking to implement your first system, Contact Us today to learn how we can help your next application.